Electromechanical Relay vs. Reed Relay: Unveiling the Distinctions
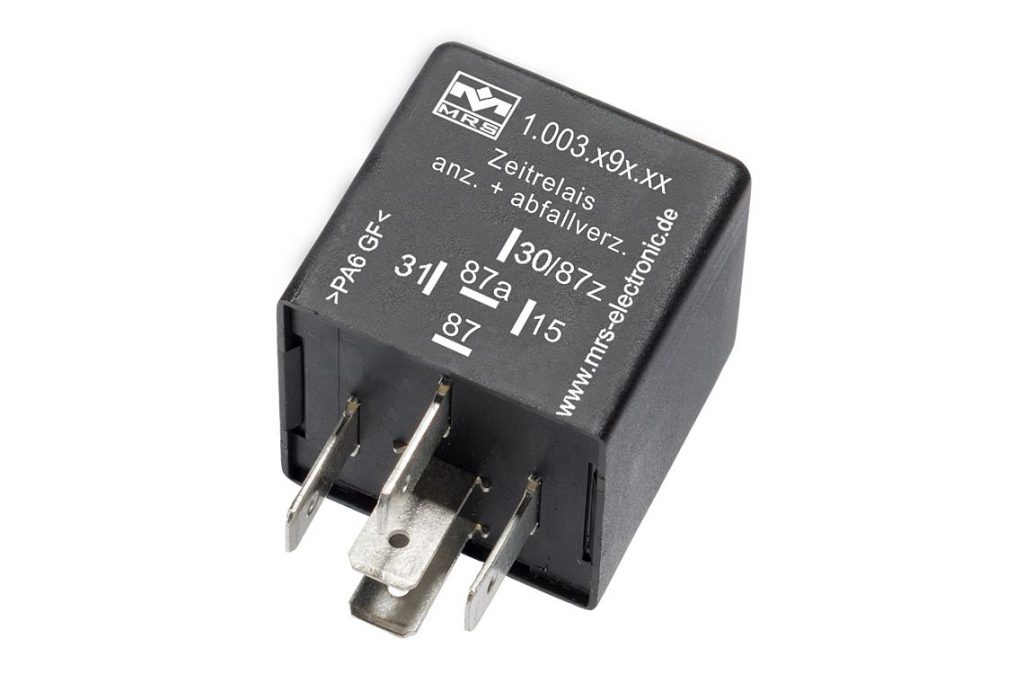
In the realm of electrical engineering, relays play a crucial role in controlling circuits and facilitating the transfer of signals. Two commonly used types of relays are electromechanical relays and reed relays. While both serve similar purposes, they differ in their construction, operation, and applications. In this article, we will delve into the intricacies of electromechanical relays and reed relays, highlighting their unique characteristics and helping you understand the key differences between them.
- Construction and Working Principle:
Electromechanical Relay:
An electromechanical relay consists of a coil, an armature, a set of contacts, and a spring. When an electrical current passes through the coil, it generates a magnetic field that attracts the armature, causing it to move and close or open the contacts. This mechanical action allows the relay to control the flow of current in a separate circuit.
Reed Relay:
In contrast, a reed relay utilizes a hermetically sealed glass tube containing two metal reeds, typically made of ferromagnetic materials. When a magnetic field is applied, the reeds attract each other, closing the contacts. Conversely, removing the magnetic field causes the reeds to separate, opening the contacts. This design offers a compact and reliable solution for switching applications.
- Size and Form Factor:
Electromechanical Relay:
Due to their mechanical components, electromechanical relays tend to be larger and bulkier compared to reed relays. They require more space and are often mounted on PCBs or in dedicated relay racks. However, their size allows for higher current and voltage ratings, making them suitable for heavy-duty applications.
Reed Relay:
Reed relays, on the other hand, are significantly smaller and more compact. Their miniature size enables them to be directly mounted on PCBs, saving valuable space in electronic devices. Despite their smaller form factor, reed relays offer excellent performance in terms of switching speed and reliability.
- Switching Speed and Lifetime:
Electromechanical Relay:
The mechanical movement involved in electromechanical relays introduces a certain amount of delay, resulting in slower switching speeds compared to reed relays. Additionally, the mechanical components are subject to wear and tear, limiting the relay's lifetime. However, electromechanical relays are capable of handling higher currents and voltages, making them suitable for applications that require robust switching capabilities.
Reed Relay:
Reed relays excel in terms of switching speed, as they rely on the magnetic attraction between the reeds, which is virtually instantaneous. This attribute makes them ideal for applications that demand rapid switching, such as telecommunications and test equipment. Furthermore, reed relays have a longer operational lifetime due to their absence of mechanical movement.
- Applications:
Electromechanical Relay:
The robustness and high current/voltage handling capabilities of electromechanical relays make them suitable for various industrial applications, including power distribution systems, motor control, and automation equipment. They are also commonly used in automotive applications, where reliability and durability are paramount.
Reed Relay:
Reed relays find their niche in applications that require compactness, high-speed switching, and low power consumption. They are extensively used in telecommunications, medical devices, instrumentation, and automated test equipment. Their ability to handle low-level signals and their excellent isolation characteristics make them invaluable in sensitive electronic circuits.
Conclusion:
In summary, electromechanical relays and reed relays differ in their construction, size, switching speed, and applications. Electromechanical relays offer robustness and high current/voltage handling capabilities, while reed relays provide compactness, rapid switching, and low power consumption. Understanding these distinctions is crucial for selecting the appropriate relay type for specific applications, ensuring optimal performance and reliability.