Gear hobbing process
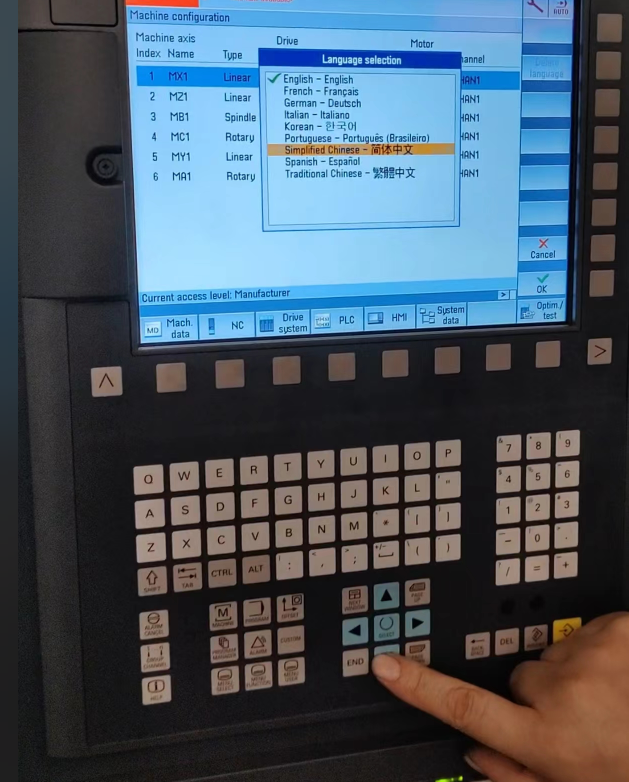
Gear hobbing is an important part of gear processing. Its process usually
includes a series of orderly steps. The following is the detailed process of
gear hobbing:
Preliminary preparation:
Ensure that the working area is clean and barrier-free, and check whether the
cooling, lubrication and hydraulic oil of the CNC gear hobbing machine are
sufficient.
Check whether the workpiece is firmly placed and whether the fixture is firm
and reliable.
Start the electrical system and wait for the machine tool to complete the
self-check.
Set processing parameters:
According to the processing requirements, set the processing parameters of
the CNC gear hobbing machine, such as gear parameters, feed speed, spindle
speed, etc.
Manual mode operation:
Switch the CNC gear hobbing machine to manual mode.
Adjust the tool and workpiece to center them.
Start the motor to rotate the tool spindle and worktable.
Use the manual operating device to bring the cutting tool close to the
workpiece and start trial cutting.
According to the predetermined feed amount, gradually move the cutting tool
to complete the preliminary processing.
Evaluate the processing quality and adjust the parameters until the
predetermined processing quality is achieved.
Automatic mode processing:
Switch the CNC gear hobbing machine to automatic mode for bulk
production.
Enter the gear hobbing program through the CNC system.
Start the CNC gear hobbing machine and start automatic processing.
Monitor various parameters during the processing, such as cutting speed, feed
speed, tool wear, etc., and adjust the processing parameters in time according
to the processing requirements.
Specific steps of gear hobbing (taking CNC system control as an example):
The C axis (workpiece rotation axis) and the B axis (hob rotation axis)
return to zero.
The B axis rotates at the entered hob speed, and the C axis rotates at the
speed adapted to the B axis.
The gear hobbing cutter is quickly positioned according to the feed point,
and the X coordinate (gear radial feed axis) moves quickly to the specified
position.
From this position, the Z coordinate (gear axial feed control axis) is
quickly positioned according to the feed point and moves quickly to another
specified position. After it is in place, the cutting fluid is turned on.
From this position, the gear root circle is positioned at a slow speed, and
the gear is slowly hobbed to another position at a predetermined feed depth.
From this position, the gear is hobbed to the end position according to the
hobbing length and hobbing feed speed.
Repeat the above steps, perform multiple feeds and hobbing until the required
tooth depth and tooth shape are achieved.
Subsequent processing:
After the processing is completed, stop the CNC gear hobbing machine.
Perform necessary cleaning and maintenance work to ensure the normal
operation of the equipment.
Inspect the processed gears to ensure that their quality meets the
requirements.
It should be noted that the operating procedures and safety specifications
must be strictly followed during the gear hobbing process to ensure the safety
of the operator and the normal operation of the equipment. At the same time,
according to different processing requirements and workpiece materials, the
process and parameters of gear hobbing may need to be adjusted and optimized
accordingly.
In addition, the quality of gear hobbing is affected by many factors, such as
the accuracy of the machine tool, the material and accuracy of the tool, the
cutting speed, the feed speed, the accuracy of the gear blank, the accuracy and
rigidity of the fixture, etc. Therefore, in the actual processing process, it is
necessary to test and adjust according to the specific situation to obtain the
best processing effect and gear quality.
www.gltmachinery.com
GLT Machinery