Unveiling the Powerhouses: Exploring the Two Types of Mechanical Fuel Pumps
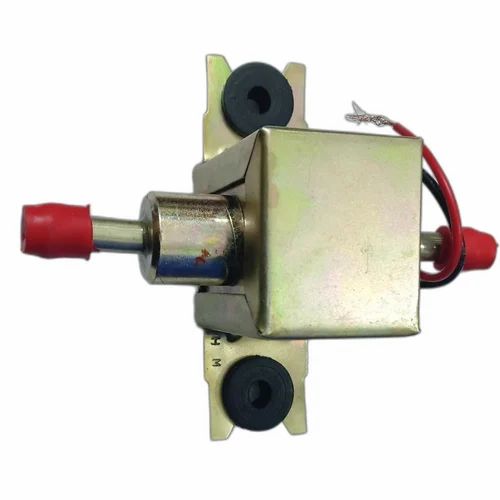
In the realm of automotive engineering, fuel delivery systems play a crucial role in ensuring optimal engine performance. Among the various types of fuel pumps, mechanical fuel pumps stand out for their reliability and simplicity. In this article, we will delve into the intricacies of mechanical fuel pumps, exploring their two primary types and shedding light on their functionalities, advantages, and applications.
- Diaphragm-Type Mechanical Fuel Pump:
The diaphragm-type mechanical fuel pump is a widely used design known for its robustness and efficiency. This pump consists of a flexible diaphragm, a lever, and a set of check valves. Here's how it works:
- Fuel Intake: As the engine rotates, the camshaft-driven lever reciprocates, creating a vacuum in the pump's chamber. This vacuum draws fuel from the tank through an inlet valve, filling the chamber.
- Fuel Discharge: When the lever moves upward, it compresses the diaphragm, forcing the fuel out through an outlet valve. The pressurized fuel then travels through the fuel lines to the carburetor or fuel injectors.
Advantages and Applications:
- Simplicity and Reliability: The diaphragm-type pump has fewer moving parts, making it less prone to mechanical failures. It is commonly used in older vehicles, small engines, and applications where simplicity and durability are paramount.
- Cost-Effectiveness: Due to its straightforward design, the diaphragm-type pump is generally more affordable than other fuel pump types. This makes it a popular choice for budget-conscious consumers and manufacturers.
- Plunger-Type Mechanical Fuel Pump:
The plunger-type mechanical fuel pump, also known as the inline fuel pump, offers enhanced performance and higher fuel delivery rates. This pump utilizes a reciprocating plunger mechanism to generate the necessary pressure. Let's explore its operation:
- Fuel Intake: Similar to the diaphragm-type pump, the plunger-type pump relies on the engine's camshaft to drive its mechanism. As the camshaft rotates, it pushes the plunger downward, creating a low-pressure area that draws fuel into the pump.
- Fuel Discharge: When the plunger moves upward, it compresses the fuel, generating high pressure. The pressurized fuel is then forced out through an outlet valve and delivered to the engine's fuel system.
Advantages and Applications:
- Higher Fuel Delivery Rates: The plunger-type pump can deliver fuel at a higher rate compared to the diaphragm-type pump. This makes it suitable for high-performance engines, heavy-duty vehicles, and applications that demand increased fuel flow.
- Precise Fuel Control: The plunger-type pump allows for more precise fuel metering, enabling better control over the air-fuel mixture. This is particularly beneficial in fuel injection systems, where accurate fuel delivery is crucial for optimal combustion.
Conclusion:
Mechanical fuel pumps, with their reliability and efficiency, continue to be an integral part of many automotive systems. Understanding the two primary types, the diaphragm-type and plunger-type pumps, provides valuable insights into their functionalities and applications. Whether it's the simplicity and durability of the diaphragm-type pump or the enhanced performance of the plunger-type pump, these powerhouses ensure the smooth and efficient delivery of fuel to keep our engines running at their best.