Decoding the Engineering Puzzle: Unraveling the Differences Between Couplings and Flanges
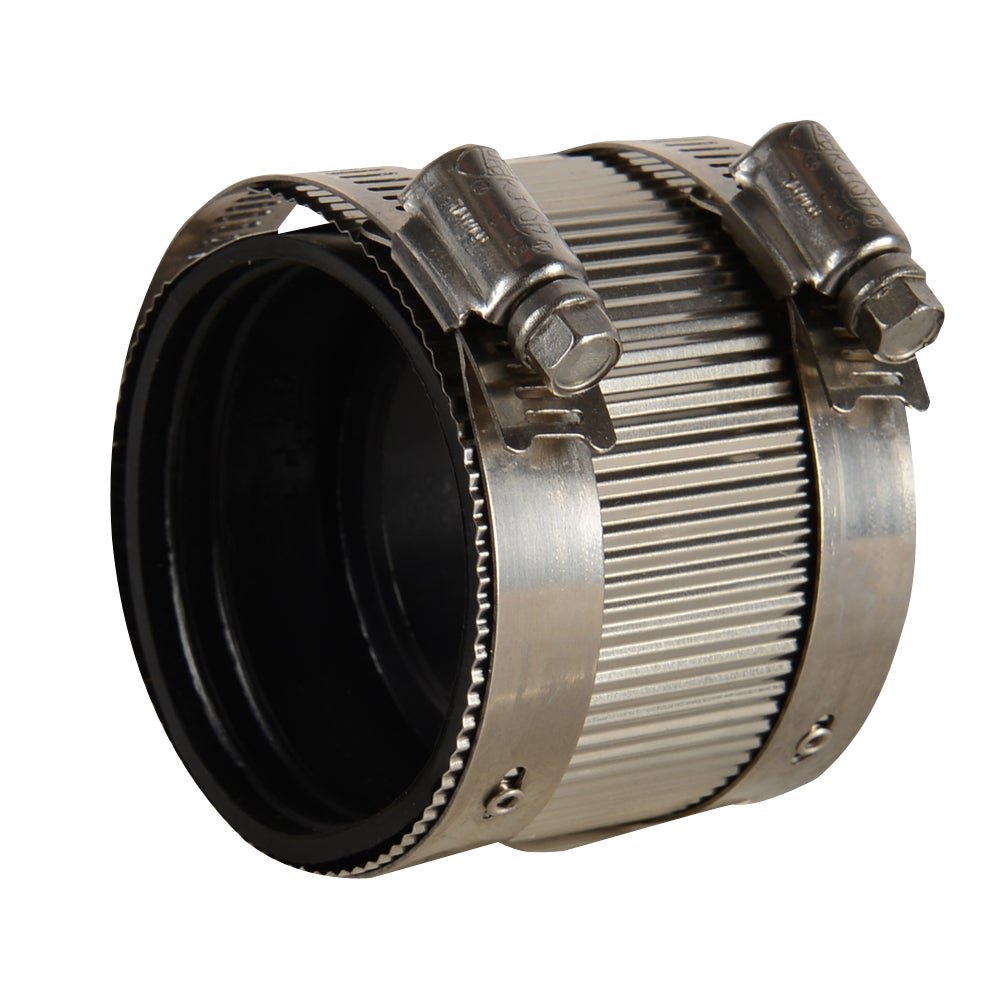
In the realm of engineering, couplings and flanges are two essential components used for connecting pipes, shafts, and other mechanical systems. While they serve similar purposes, there are distinct differences between the two. In this article, we will delve into the intricacies of couplings and flanges, exploring their functions, designs, applications, and key differentiating factors.
- Couplings:
Couplings are mechanical devices used to connect two shafts or pipes together, transmitting torque, motion, or fluid between them. They provide a flexible or rigid connection, depending on the specific requirements of the system. Here are some key aspects of couplings:
1.1. Types of Couplings:
There are various types of couplings, including:
1.1.1. Flexible Couplings:
Flexible couplings compensate for misalignment between shafts, absorb shocks and vibrations, and allow for angular and axial movement. Examples include elastomeric couplings, gear couplings, and grid couplings. They find applications in motor-driven systems, pumps, compressors, and conveyor systems.
1.1.2. Rigid Couplings:
Rigid couplings provide a solid connection between shafts, offering high torque transmission and precise alignment. They are commonly used in applications where shaft misalignment is minimal, such as precision machinery, robotics, and power transmission systems.
1.2. Design and Installation:
Couplings are typically designed to accommodate specific torque, speed, and misalignment requirements. Factors such as shaft size, material compatibility, and environmental conditions influence the selection and installation of couplings. Proper alignment, lubrication, and maintenance are crucial for ensuring optimal performance and longevity.
- Flanges:
Flanges are flat, circular discs with evenly spaced bolt holes used to connect pipes, valves, and other equipment. They provide a secure and leak-proof connection, allowing for easy assembly and disassembly. Here are some key aspects of flanges:
2.1. Types of Flanges:
There are several types of flanges, including:
2.1.1. Weld Neck Flanges:
Weld neck flanges have a long tapered hub, which provides reinforcement and facilitates smooth flow transition. They are commonly used in high-pressure and high-temperature applications, such as oil and gas pipelines, petrochemical plants, and power generation facilities.
2.1.2. Slip-On Flanges:
Slip-on flanges slide over the pipe and are then welded in place. They are cost-effective and suitable for low-pressure applications. Slip-on flanges are commonly used in water supply systems, HVAC systems, and low-pressure piping networks.
2.2. Design and Installation:
Flanges are designed to withstand specific pressure ratings, temperature ranges, and fluid types. Factors such as flange material, gasket selection, and bolt tightening torque significantly impact the sealing performance. Proper alignment, bolt tightening sequence, and gasket maintenance are crucial for preventing leaks and ensuring system integrity.
- Key Differences:
Now, let's highlight the key differences between couplings and flanges:
3.1. Function:
Couplings primarily transmit torque, motion, or fluid between shafts or pipes, while flanges provide a secure connection and facilitate easy assembly and disassembly of pipes and equipment.
3.2. Flexibility:
Couplings offer flexibility, allowing for misalignment compensation and vibration absorption, while flanges provide a rigid connection.
3.3. Applications:
Couplings are commonly used in rotating machinery, power transmission systems, and fluid handling applications. Flanges are prevalent in piping systems, process industries, and infrastructure projects.
3.4. Design:
Couplings are designed to accommodate shaft misalignment, torque transmission, and specific motion requirements. Flanges are designed to withstand pressure, temperature, and fluid compatibility.
Conclusion:
In summary, couplings and flanges are vital components in engineering systems, each serving distinct purposes. Couplings enable torque transmission and compensate for misalignment, while flanges provide a secure connection and facilitate easy assembly and disassembly of pipes. By understanding their functions, designs, and applications, engineers can make informed decisions when selecting the appropriate component for their specific needs.