The Advantages of Welding over Riveting: A Comprehensive Analysis
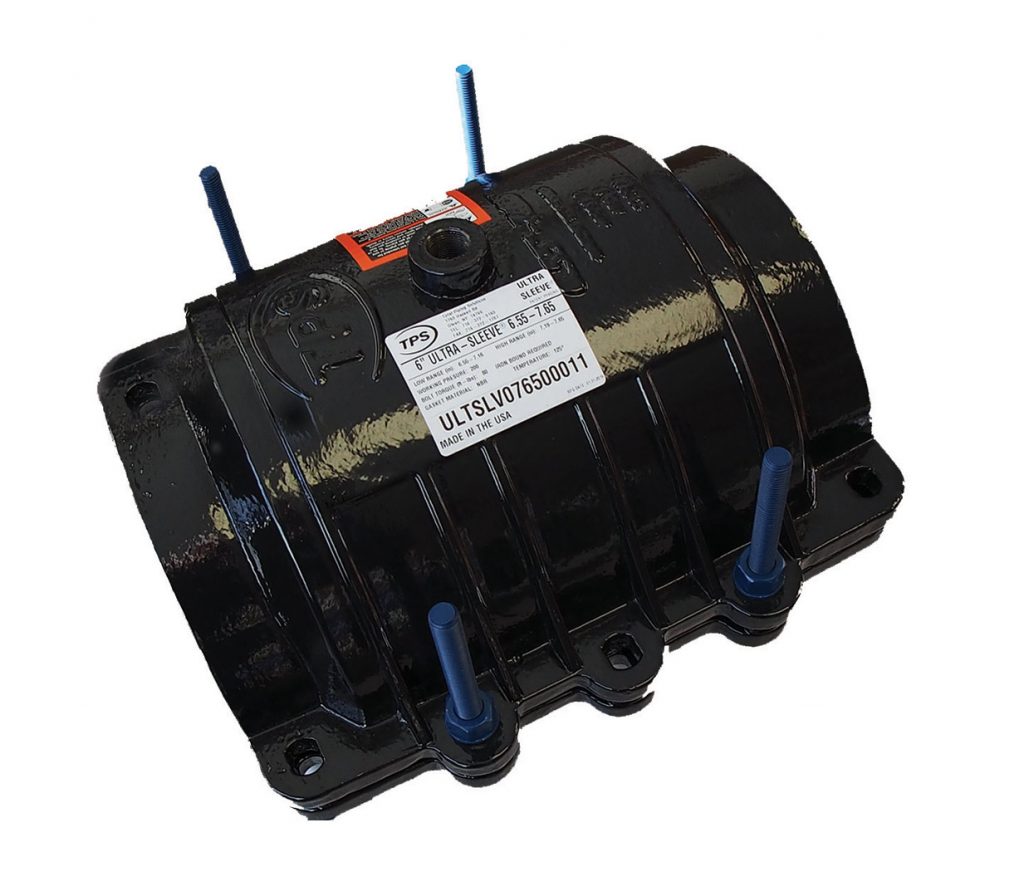
In the field of engineering, the choice between welding and riveting plays a crucial role in joining metal components. While both methods have their merits, welding has emerged as a superior technique in many aspects. This article aims to explore the reasons why welding is considered better than riveting, highlighting its advantages in terms of strength, efficiency, versatility, and cost-effectiveness.
- Superior Strength and Structural Integrity:
Welding offers unparalleled strength and structural integrity compared to riveting. By melting and fusing the base metals, welding creates a continuous joint that distributes the load evenly. This results in a joint that is often stronger than the base materials themselves, making it ideal for applications that require high durability and load-bearing capacity. - Enhanced Efficiency and Time Savings:
When it comes to efficiency, welding outshines riveting in several ways. Firstly, welding eliminates the need for additional fasteners like rivets, bolts, or screws, reducing the overall assembly time. Secondly, the welding process allows for simultaneous joining of multiple components, enabling faster production rates. Additionally, the absence of protruding fasteners in welded joints minimizes the need for post-joining finishing operations, further saving time and effort. - Versatility and Design Flexibility:
Welding offers unparalleled versatility and design flexibility, making it suitable for a wide range of applications. Unlike riveting, which requires access to both sides of the joint, welding can be performed from a single side, allowing for greater accessibility in complex structures. Moreover, welding enables the joining of dissimilar metals, expanding the possibilities for material combinations and facilitating the creation of innovative designs. - Cost-effectiveness and Long-term Savings:
While welding may involve higher initial equipment and labor costs compared to riveting, it often proves to be more cost-effective in the long run. Welded joints have a longer lifespan and require minimal maintenance, reducing the need for frequent repairs or replacements. Additionally, the superior strength of welded joints allows for the use of lighter and thinner materials, resulting in material cost savings over time.
Conclusion:
In conclusion, welding surpasses riveting in various aspects, making it the preferred choice for joining metal components in many engineering applications. Its superior strength, enhanced efficiency, versatility, and long-term cost-effectiveness make welding a valuable technique. By understanding the advantages of welding over riveting, engineers and manufacturers can make informed decisions when selecting the most suitable joining method for their specific requirements.